- Continental
- Electronic Stability Control
- ESC
- Anti-lock Brake Systems
- ABS
- Wheel Speed Sensors
- WSS
- Vision Zero
- Anudeep Garg
- Sukhdeep Sandhu
Continental’s Gurgaon Plant Attains New Production Milestone for EBS And WSS
- By MT Bureau
- September 13, 2024
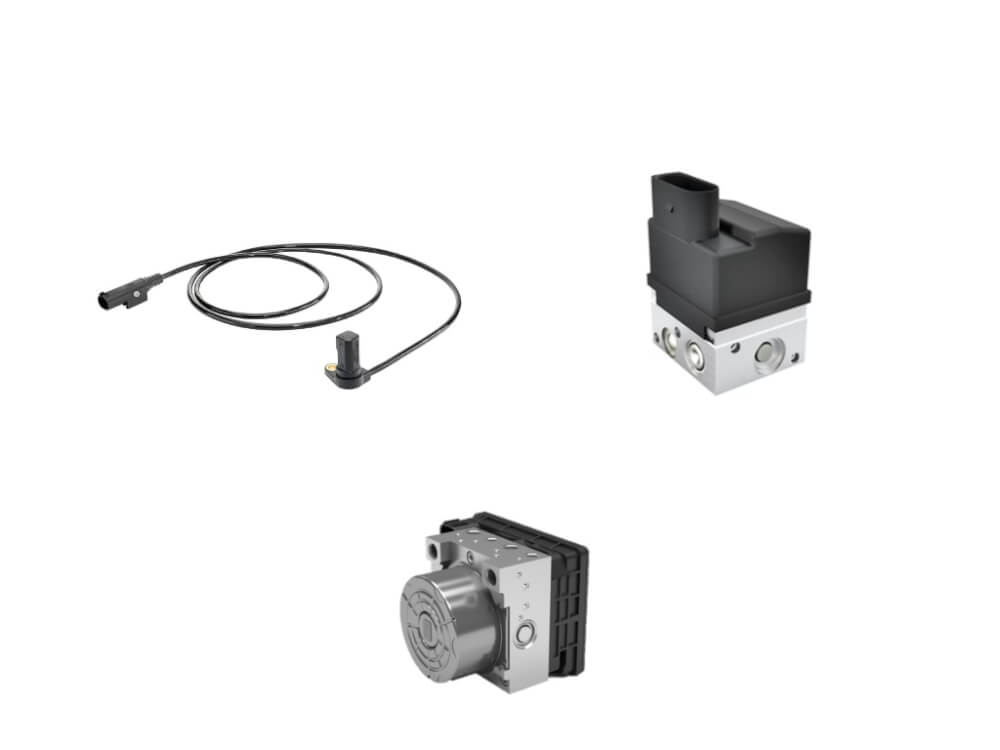
German tier 1 supplier Continental’s Gurgaon plant has attained a new production milestone of producing 10 million Electronic Brake Systems (EBS) and 100 million Wheel Speed Sensors (WSS), two components integral to the safety of a vehicle.
The EBS portfolio comprises Electronic Stability Control (ESC) for passenger cars and Anti-lock Brake Systems (ABS) for both, passenger cars and two-wheelers. It provides directional stability and steerability of the vehicle whereas, ABS aims to avoid locking of the wheels and keeps the vehicle steerable during braking. Additionally, the signals from the WSS are required for control systems like Anti-lock Braking System (ABS) and Electronic Stability Control (ESC).
The company states that over 1.3 million people loose their lives in road accidents worldwide every year and more than 50 million are injured. In India, 53 accidents and 19 deaths occur every hour, or an average of 1,264 accidents and 42 deaths daily due to road crashes, according to a Ministry of Road Transport and Highways report in 2023. To enhance road safety in the country, ABS technology was made mandatory in 2019, followed by a proposal for ESC in 2022 by the government.
Sukhdeep Sandhu, Head of Safety and Motion, Continental Automotive India said, “Safety is non-negotiable. At Continental, we have consistently brought relevant technologies to the market for our customers, helping make vehicles and thereby our roads safer. Our expertise in active and passive safety systems is a key driver in reducing the number of traffic-related fatalities, injuries, and road accidents”.
“Localisation is at the core of company’s strategy in India. Supported by legislations which have played a huge role in ensuring vehicular safety, we have been able to localise both production and R&D, ensuring greater value to our customers in the market. Customers in India are proactive in their adoption approach towards safety technologies”, he added.
Continental’s ‘Vision Zero’ is focussing on ensuring zero road fatalities, injuries and crashes, through technologies, components and systems and ongoing innovations.
The tier 1 supplier is also one of the largest manufacturers of WSS in India. Apart from catering to leading OEMs in India, these components are also exported to other Asian and European regions.
Anudeep Garg, Head of the Gurgaon plant, Continental Automotive India said, “We are proud to achieve this milestone and continue to focus on localisation. As a Tier 1 supplier, we follow global manufacturing standards and have adopted several advanced technologies to create a digital shopfloor. Additionally, industry 4.0 technologies enable us to not only maintain product quality and enhance efficiency but also to effectively streamline our supply chain. We aim to increase the manufacturing capacity of EBS and WSS in double-digit percentages in the next three years for both passenger vehicles as well two-wheelers.”
Continental’s ‘in the market, for the market’ approach has seen its entire value chain from R&D to design and production being localised. This way Continental is focusing on enabling easy access to safety products by adapting globally proven technologies to suit the local market. Wide-scale production offers economy of scale and ensures cost advantage, thereby contributing to increased democratization of safety features in vehicles across segments in India.
It was in 2016, when Continental set up assembly lines in Gurugram for Antilock Brake Systems (ABS) and Electronic Stability Control (ESC) systems for two-wheelers and passenger cars. In 2018, it commenced production for ABS and ESC Electronic Control Units (ECU) at its Bengaluru plant. In the subsequent year, the company achieved the production milestone of one million ABS and ESC ECUs at its Bengaluru plant, and in 2020, reached a milestone of 50 Million Wheel Speed Sensors (WSS) at its Manesar plant. Additionally, Continental entered into a joint venture with Japanese firm Nisshinbo Holdings in 2022, to localise machining for valve blocks for Electronic Brake Systems (EBS) in India.
- SSAB
- Polmotors
- fossil-free materials
- decarbonised steel
- Vattenfall
- LKAB
- Volkswagen
- Audi
- BMW
- Peugeot
- Citroen
- Jeep
- Stellantis
- Mercedes-Benz
- Opel
- Maciej Grabos
- Robert Lewandowski
SSAB Partners Polmotors To Introduce Fossil-Free Steel Structural Automotive Components
- By MT Bureau
- June 27, 2025

Swedish steel manufacturer SSAB has announced a new collaboration with Polmotors, a tier 1 supplier focusing on low-emission products, for exploring the potential of fossil-free materials in demanding automotive applications.
The partnership will see Polmotors explore manufacturing components using SSAB’s decarbonised steel.
SSAB is working on two unique decarbonised steels and aims to largely eliminate carbon dioxide emissions from its own operations. It has already introduced SSAB Zero, which is based on recycled steel and made using fossil-free energy. The company claims that it has also successfully produced the world’s first fossil-free steel. It works with iron ore producer LKAB and energy company Vattenfall as part of the HYBRIT initiative to develop a value chain for fossil-free iron- and steel production, replacing the coking coal traditionally used for iron ore-based steelmaking with fossil-free electricity and hydrogen. This process virtually eliminates carbon dioxide emissions in steel production.
On the other hand, Polmotors closely works with the likes of Volkswagen, Audi, BMW, Peugeot, Citroen, Jeep, Stellantis, Mercedes-Benz and Opel among others, to introduce high-performance components which are not only lighter but also greener.
Maciej Grabos, CEO, Polmotors, said, “Polmotors sees the future of fossil-free steel. And the potential competitive advantage of being an early adopter, positioning ourselves to meet the anticipated market demand from premium automotive OEMs. We design and manufacture crash management systems (CMSs) for these customers, such as bumpers and rally bars, so choice of materials is crucial. Polmotors looks forward to joint R&D – working with SSAB and the OEMs – for the implementation of new steel grades in our products.”
Robert Lewandowski, Key Account Manager, SSAB, said, “Polmotors recently celebrated its 35thanniversary. I’ve had the pleasure and privilege to meet them 20 years ago and observe how an initially small, Polish-owned enterprise turned into a global Tier1 supplier. Decarbonisation of the automotive industry requires cooperation across the supply chain where Tier 1 companies play an important role”.
- Ministry of Heavy Industries
- HD Kumaraswamy
- Narendra Modi
- Scheme to Promote Manufacturing of Electric Passenger Cars in India
Heavy Industry Ministry Rolls Out Scheme To Promote EV Manufacturing In India
- By MT Bureau
- June 25, 2025
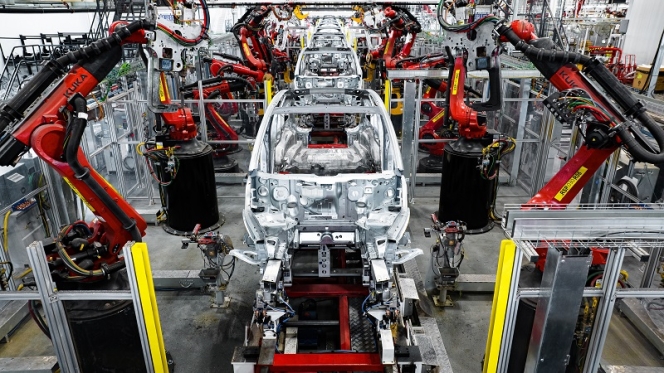
The Ministry of Heavy Industries (MHI) has announced a new initiative to promote green mobility in the country under the ‘Scheme to Promote Manufacturing of Electric Passenger Cars in India’ (SPMECI).
The initiative aims to focus on encouraging the manufacturing of electric four-wheelers in the country. The scheme eventually looks to establish India as a premier global EV-manufacturing hub and attract investments from global electric vehicle companies, along with generating employment.
The Ministry of Heavy Industry has opened the application portal for a period of around 3 months starting from 24 June 2025 till 6pm on 21st October 2025.
HD Kumaraswamy, Union Minister for Heavy Industries and Steel of India, said, “Guided by the visionary leadership of Prime Minister Narendra Modi, this initiative marks a defining moment in India’s journey towards clean, self-reliant and future-ready mobility. The launch of this portal under the SPMEPCI scheme opens new avenues for global electric vehicle manufacturers to invest in India’s rapidly evolving automotive landscape. This scheme not only supports our national commitment to achieving Net Zero by 2070, but also reinforces our resolve to build a sustainable, innovation-driven economy.”
As per the guidelines, all approved applicants will need to invest a minimum of INR 41.5 billion to establish long-term manufacturing footprints in India. Global OEMs who invest in the country will be able to import electric passenger vehicles as Completely Built Units (CBUs) with a minimum CIF value of USD 35,000 at reduced customs duty of 15 percent for a period of five years from the Application Approval Date.
The Ministry has announced calibrated customs duty concessions and clearly defined Domestic Value Addition (DVA) milestones to strike a balance between the introduction of advanced EV technologies and the use of indigenous capabilities. Through domestic value addition targets, the scheme aims to fast track global and domestic companies towards becoming active partners in the country’s green mobility revolution.
SPMECI had been notified by a notification given on 15 March 2024.
Tata Motors Inaugurates Re.Wi.Re Facility In Lucknow And Raipur
- By MT Bureau
- June 19, 2025
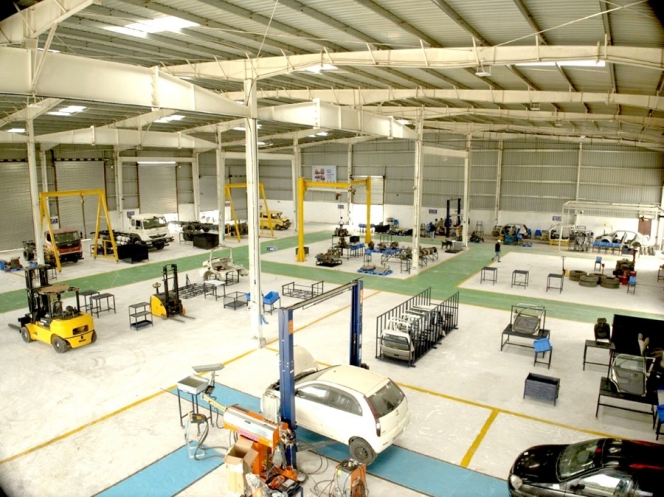
Tata Motors, one of India’s leading automobile manufacturers, has inaugurated two—state-of-the-art Re.Wi.Re – Recycle with Respect – Registered Vehicle Scrapping Facilities (RVSFs) in Lucknow, Uttar Pradesh and Raipur, Chhattisgarh.
The Union Minister of Road Transport and Highways, Government of India, Nitin Gadkari, inaugurated these facilities virtually. The facilities are designed to safely and responsibly dismantle end-of-life vehicles including two-wheelers, three-wheelers, passenger vehicles and commercial vehicles, irrespective of the brands.
Nitin Gadkari, said, “I am pleased to launch two Registered Vehicle Scrapping Facilities in Lucknow and Raipur. These modern centres mark a progressive step under the National Vehicle Scrappage Policy, which empowers citizens to transition to cleaner, more fuel-efficient vehicles through structured incentives. These facilities will play a crucial role in the safe dismantling of unfit vehicles while enabling the recovery of valuable materials for scientific recycling. I commend Tata Motors for their steadfast commitment to sustainability and for establishing a nationwide RVSF infrastructure that aligns with global standards. Progressive initiatives like these are vital to building a robust ecosystem that makes vehicle scrappage accessible, efficient, and impactful across the country.”
The Raipur facility has a capacity to process 25,000 vehicles per annum, while Lucknow facility can scrap upto 15,000 vehicles annually.
Girish Wagh, Executive Director, Tata Motors, said, “Sustainability is not merely a commitment at Tata Motors—it is a foundational pillar shaping the future of mobility. Guided by the principles of a circular economy, we are steadfast in our pursuit of responsible and eco-friendly practices. With the widest nationwide network of Re.Wi.Re facilities, Tata Motors is now equipped to responsibly dismantle over 175,000 end-of-life vehicles annually. We deeply value the unwavering support and collaboration of our partners, state governments, and local authorities in turning this vision into reality. I would especially like to thank Union Minister Nitin Gadkari for his continued leadership and encouragement in advancing sustainable mobility and vehicle recycling in India.”
With this, Tata Motors now has 10 vehicle scrapping centres across the country including - Jaipur, Bhubaneswar, Surat, Chandigarh, Delhi-NCR, Pune, Guwahati, Raipur, Lucknow and Kolkata.
May Auto Sales Remains Muted, Cheaper Loans & Above Normal Monsoon May Drive Growth
- By MT Bureau
- June 16, 2025
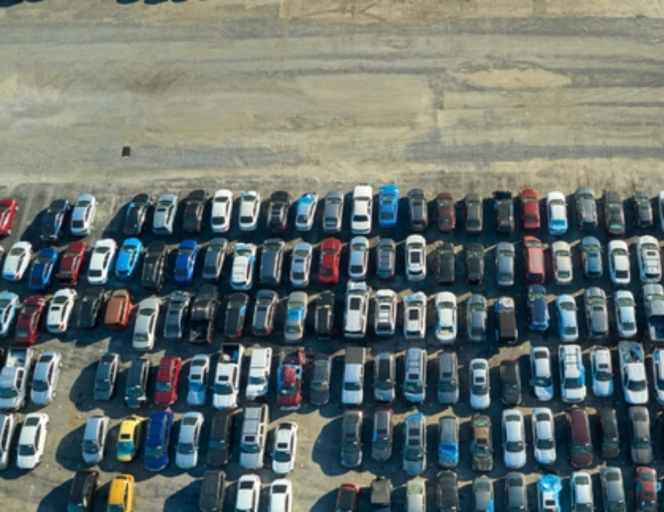
The Society of Indian Automobile Manufacturers (SIAM), the apex body representing automakers in India, has announced the wholesale data for May 2025. The month gone by saw a total of 2.05 million vehicles sold across the two-wheeler, three-wheeler and four-wheeler categories. This marked a flat growth versus 2.02 million vehicles sold last year, but an 11 percent growth over April 2025.
Looking at the segment-wise sales, the passenger vehicle sales were primarily driven by the robust demand for SUVs with 196,821 units sold, up 7.6 percent, as compared to 182,883 units sold last year. On the other hand, passenger car sales declined by 12.2 percent with 93,951 units sold, as compared to 106,952 units sold last year.
The three-wheeler segment was in the red across segments, with a total of 53,942 units sold, down 3.3 percent YoY.
In the two-wheeler space, the wholesales for motorcycles remained flat at 1.03 million units sold, while scooter sales grew by 7 percent at 579,507 units sold as compared to 540,866 units sold last year.
Commenting on the sales data, Rajesh Menon, Director General, SIAM, said, “All vehicle segments posted stable performance in May 2025. Passenger Vehicles segment posted sales of 3.45 lakh units, though 2nd highest ever of May, the segment de-grew marginally by 0.8 percent compared to May 2024, three-wheelers de-grew by 3.3 percent compared to May of previous year, with sales of 0.54 lakh units, while two-wheeler segment grew by 2.2 percent in May 2025, as compared to May 2024, with sales of 16.56 lakh units. Going forward, the RBI’s three repo rate cuts totalling 100 basis points in less than six months, along with a forecast of above-normal monsoons are some of the indicators which should positively impact the auto sector by improving affordability and boosting consumer sentiment in the coming months.”
Comments (0)
ADD COMMENT