Middle East Situation Likely To Strain Supply Chains
- By Bhushan Mhapralkar
- October 05, 2024
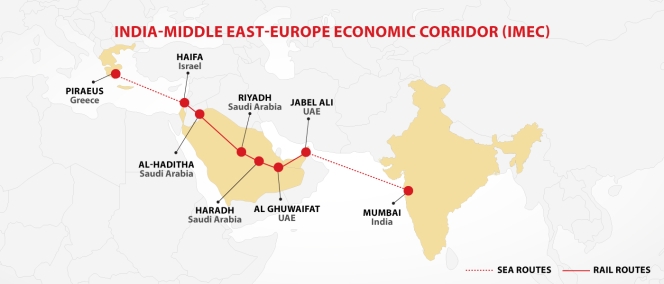
With the share market in India showing signs of being affected by the developments in the Middle East, it is quite likely that the supply chains, including those that influence the auto industry, will see some signs of strain eventually if not at once.
The likely reasons for this is the effect of an escalation in crude oil prices primarily. The others would involve shipping route disruptions such that the cargo ships carrying automotive parts, tools and equipment are unable to navigate their usual shipping lanes. This would result in delays and cost escalation as longer routes are chosen for safe passage. The example of Tesla and Volvo suspending manufacturing in early 2024 due to the conflict in the Red Sea is not yet lost.
In terms of trade and tariffs, the conflicts and tensions between countries can be detrimental. The cost for manufacturers using materials like steel and aluminum can escalate at a rapid pace.
With the Middle East known for its oil reserves, the current conflict and the way it is progressing is already having an effect on the crude prices. If it gets bad than this, large importing markets like India could see their crude import bills rise further. As it is, the prices of fossil fuels are already high with over 200 percent taxes.
Any disruption in oil supply will impart considerable volatility, transportation cost increase and strain on an economy that is already fighting post-Covid inflation.
Image for representative purpose only
- Skoda Auto Volkswagen India
- Skoda India
- Octavia
- Laura
- Superb
- Kodiaq
- Kushaq
- Slavia
- Kylaq
- Andreas Dick
- Piyush Arora
Skoda Auto Volkswagen Rolls Out 500,000th Made In India Skoda Car
- By MT Bureau
- July 04, 2025
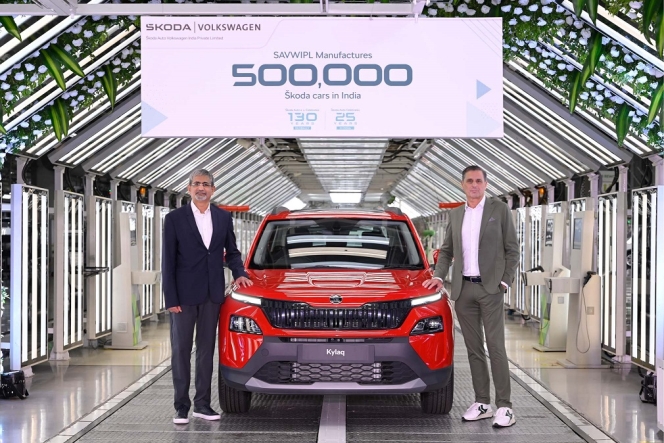
Skoda Auto Volkswagen India has announced that it has achieved a major manufacturing milestone in its operations. The company recently rolled out its 500,000th made-in-India Skoda vehicle.
The milestone comes after 24 years since the company introduced the first Skoda Octavia from its Chhatrapati Sambhaji Nagar facility (formerly Aurangabad) in 2001.
At present, the company manufactures vehicles across two facilities in India – Chhatrapati Sambhaji Nagar and Pune, with them now supporting the company’s new manufacturing plant in Vietnam with parts and components.
Over the years, Skoda has rolled out its iconic products such as Octavia, Laura, Superb and Kodiaq to new products like the Kushaq, Slavia and its first sub-4-meter Kylaq.
Andreas Dick, Board Member for Production and Logistics, Skoda Auto, said, “Reaching the milestone of 500,000 cars produced in India is a proud testament to our strategic vision of unwavering commitment to India and operational excellence. By nurturing local engineering talent and embedding global manufacturing processes, we’ve built an ecosystem that is agile, scalable, and responsive to a dynamically changing environment that meets the highest international standards. This achievement reflects the synergy between world-class innovation and India’s growing industrial prowess.”
Piyush Arora, CEO & Managing Director, Skoda Auto Volkswagen India, said, “It is not just about manufacturing 500,000 cars, but building and nurturing 500,000 connections. Every car that rolls out of our production lines, shares DNA of European engineering with unmatched quality, crafted with precision; delivering supreme comfort, safety, technology and driving dynamics. This achievement belongs as much to our customers as it does to our employees. Because what we’re manufacturing here isn’t just mobility, it’s a belief in what India can make for domestic as well as international markets. India plays a pivotal role in the Group’s growth strategy. I am glad to mention that we achieve this manufacturing milestone in the same year as Skoda Auto celebrates 130 years of legacy globally and 25 years of presence in India.”
The company revealed that approximately 70 percent of the vehicles manufactured in India were rolled out from its Chhatrapati Sambhaji Nagar plant.
Shell Lubricants Acquires Raj Petro From Brenntag Group To Further Expand Lubricants Business
- By MT Bureau
- July 03, 2025
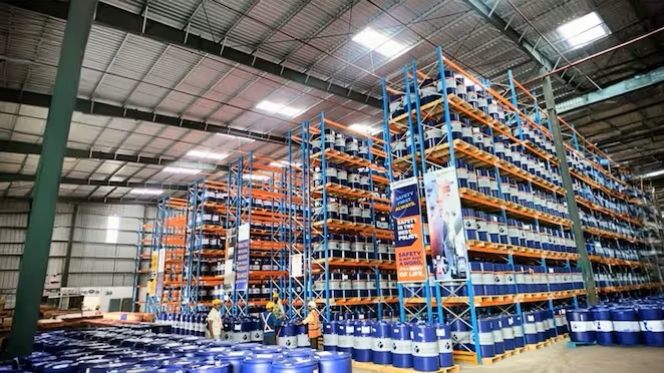
Shell Lubricants, the lubricants business of UK-headquartered Shell Group of companies, has acquired 100 percent equity stake in Raj Petro Specialities from Brenntag Group.
India is currently the world’s third-largest lubricant market and this initiative Shell expects to further expand its portfolio and customer base in the country, but also enhance its presence in the global markets.
Raj Petro is a multi-faceted petrochemical manufacturing and marketing company with business partners in about 100 countries across the globe and offers a wide range of products catering to power, energy, transport, construction, automotive, personal care, food, agriculture, pharmaceutical and other industries.
The acquisition of Raj Petro Specialities supports Shell Lubricants as it strives to grow its portfolio and customer base in India, which is one of its key growth markets.
Jason Wong, Executive Vice-President for Global Lubricants, Shell, said, “The addition of Raj Petro Specialities will help maximise value for Shell through a complementary product portfolio and increased scale of business, positioning Shell Lubricants for further growth in line with our unwavering focus on performance, discipline, and simplification.”
- SSAB
- Polmotors
- fossil-free materials
- decarbonised steel
- Vattenfall
- LKAB
- Volkswagen
- Audi
- BMW
- Peugeot
- Citroen
- Jeep
- Stellantis
- Mercedes-Benz
- Opel
- Maciej Grabos
- Robert Lewandowski
SSAB Partners Polmotors To Introduce Fossil-Free Steel Structural Automotive Components
- By MT Bureau
- June 27, 2025

Swedish steel manufacturer SSAB has announced a new collaboration with Polmotors, a tier 1 supplier focusing on low-emission products, for exploring the potential of fossil-free materials in demanding automotive applications.
The partnership will see Polmotors explore manufacturing components using SSAB’s decarbonised steel.
SSAB is working on two unique decarbonised steels and aims to largely eliminate carbon dioxide emissions from its own operations. It has already introduced SSAB Zero, which is based on recycled steel and made using fossil-free energy. The company claims that it has also successfully produced the world’s first fossil-free steel. It works with iron ore producer LKAB and energy company Vattenfall as part of the HYBRIT initiative to develop a value chain for fossil-free iron- and steel production, replacing the coking coal traditionally used for iron ore-based steelmaking with fossil-free electricity and hydrogen. This process virtually eliminates carbon dioxide emissions in steel production.
On the other hand, Polmotors closely works with the likes of Volkswagen, Audi, BMW, Peugeot, Citroen, Jeep, Stellantis, Mercedes-Benz and Opel among others, to introduce high-performance components which are not only lighter but also greener.
Maciej Grabos, CEO, Polmotors, said, “Polmotors sees the future of fossil-free steel. And the potential competitive advantage of being an early adopter, positioning ourselves to meet the anticipated market demand from premium automotive OEMs. We design and manufacture crash management systems (CMSs) for these customers, such as bumpers and rally bars, so choice of materials is crucial. Polmotors looks forward to joint R&D – working with SSAB and the OEMs – for the implementation of new steel grades in our products.”
Robert Lewandowski, Key Account Manager, SSAB, said, “Polmotors recently celebrated its 35thanniversary. I’ve had the pleasure and privilege to meet them 20 years ago and observe how an initially small, Polish-owned enterprise turned into a global Tier1 supplier. Decarbonisation of the automotive industry requires cooperation across the supply chain where Tier 1 companies play an important role”.
- Ministry of Heavy Industries
- HD Kumaraswamy
- Narendra Modi
- Scheme to Promote Manufacturing of Electric Passenger Cars in India
Heavy Industry Ministry Rolls Out Scheme To Promote EV Manufacturing In India
- By MT Bureau
- June 25, 2025
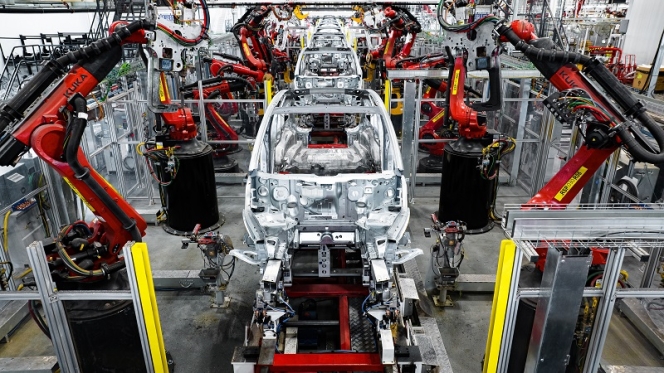
The Ministry of Heavy Industries (MHI) has announced a new initiative to promote green mobility in the country under the ‘Scheme to Promote Manufacturing of Electric Passenger Cars in India’ (SPMECI).
The initiative aims to focus on encouraging the manufacturing of electric four-wheelers in the country. The scheme eventually looks to establish India as a premier global EV-manufacturing hub and attract investments from global electric vehicle companies, along with generating employment.
The Ministry of Heavy Industry has opened the application portal for a period of around 3 months starting from 24 June 2025 till 6pm on 21st October 2025.
HD Kumaraswamy, Union Minister for Heavy Industries and Steel of India, said, “Guided by the visionary leadership of Prime Minister Narendra Modi, this initiative marks a defining moment in India’s journey towards clean, self-reliant and future-ready mobility. The launch of this portal under the SPMEPCI scheme opens new avenues for global electric vehicle manufacturers to invest in India’s rapidly evolving automotive landscape. This scheme not only supports our national commitment to achieving Net Zero by 2070, but also reinforces our resolve to build a sustainable, innovation-driven economy.”
As per the guidelines, all approved applicants will need to invest a minimum of INR 41.5 billion to establish long-term manufacturing footprints in India. Global OEMs who invest in the country will be able to import electric passenger vehicles as Completely Built Units (CBUs) with a minimum CIF value of USD 35,000 at reduced customs duty of 15 percent for a period of five years from the Application Approval Date.
The Ministry has announced calibrated customs duty concessions and clearly defined Domestic Value Addition (DVA) milestones to strike a balance between the introduction of advanced EV technologies and the use of indigenous capabilities. Through domestic value addition targets, the scheme aims to fast track global and domestic companies towards becoming active partners in the country’s green mobility revolution.
SPMECI had been notified by a notification given on 15 March 2024.
Comments (0)
ADD COMMENT