- Mercedes-Benz
- electric vehicle
- battery recycling
- cobalt
- nickel
- lithium
- aluminium
- iron
- carbon black
- Jorg Burzer
- Thekla Walker MdL
- Ola Scholz
- Ola Kaellenius
Mercedes-Benz Opens Europe’s First Battery Recycling Plant In Germany
- By MT Bureau
- October 22, 2024
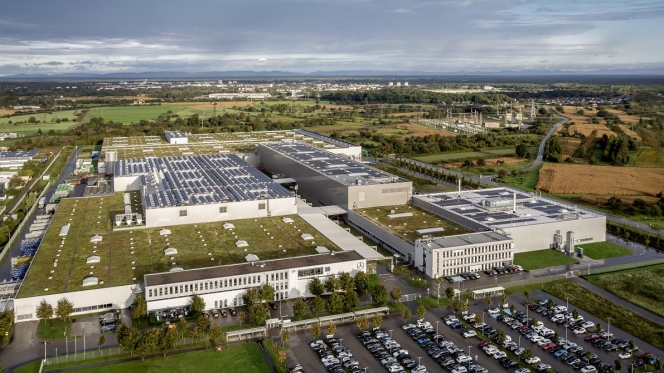
German luxury carmaker Mercedes-Benz has opened Europe's first battery recycling plant with an integrated mechanical-hydrometallurgical process making it the first car manufacturer worldwide to close the battery recycling loop with its own in-house facility.
The recycling plant in Kuppenheim, southern Germany, creates a genuine circular economy. Unlike existing established processes, the expected recovery rate of the mechanical-hydrometallurgical recycling plant is more than 96 percent. Valuable and scarce raw materials such as lithium, nickel and cobalt can be recovered – in a way which is suitable for use in new batteries for future all-electric Mercedes-Benz vehicles. The company has invested tens of millions of euros in the construction of the new battery recycling plant and thus in the value creation in Germany. Federal Chancellor Olaf Scholz and Baden-Württemberg's Environment Minister Thekla Walker visited the plant for the opening ceremony in Kuppenheim, Baden.
Ola Kaellenius, Chairman of the Board of Management, Mercedes-Benz Group said, “Mercedes-Benz has set itself the goal of building the most desirable cars in a sustainable way. As a pioneer in automotive engineering, Europe's first integrated mechanical-hydrometallurgical battery recycling factory marks a key milestone towards enhancing raw-materials sustainability. Together with our partners from industry and science, we are sending a strong signal of innovative strength for sustainable electric mobility and value creation in Germany and Europe.”
Ola Scholz said, “The future of the automobile is electric, and batteries are an essential component of this. To produce batteries in a resource-conserving and sustainable way, recycling is also key. The circular economy is a growth engine and, at the same time, an essential building block for achieving our climate targets! I congratulate Mercedes-Benz for its courage and foresight shown by this investment in Kuppenheim. Germany remains a cutting-edge market for new and innovative technologies.”
The luxury carmaker has joined hands with Primobius, a joint venture between German plant and mechanical engineering company SMS Group and Asutralian process technology developer Neometals, which is its technology partner for the battery recycling factory.
The plant is receiving funding from the German Federal Ministry for Economic Affairs and Climate Action as part of a scientific research project with three German universities. The project looks at the entire process chain for recycling, including logistics and reintegration concepts. The partners are thus making an important contribution to future scaling of the battery recycling industry in Germany.
Integrated mechanical-hydrometallurgical
For the first time in Europe, the Mercedes-Benz battery recycling plant covers all steps from shredding battery modules to drying and processing active battery materials. The mechanical process sorts and separates plastics, copper, aluminium and iron in a complex, multi-stage process. The downstream hydrometallurgical process is dedicated to the so-called black mass. These are the active materials that make up the electrodes of the battery cells. The valuable metals cobalt, nickel and lithium are extracted individually in a multi-stage chemical process. These recyclates are of battery quality and therefore suitable for use in the production of new battery cells.
Unlike the pyrometallurgy established in Europe at present, the hydrometallurgical process is less-intensive in terms of energy consumption and material waste. Its low process temperatures of up to 80deg Celsius mean it consumes less energy. In addition, like all Mercedes-Benz production plants, the recycling plant operates in a net carbon-neutral manner. It is supplied with 100 percent green electricity. The roof area of the 6800 square-metre building is equipped with a photovoltaic system with a peak output of more than 350 kilowatts.
The Mercedes-Benz battery recycling plant in Kuppenheim has an annual capacity of 2,500 tonnes. The recovered materials feed into the production of more than 50,000 battery modules for new all-electric Mercedes-Benz models. The knowledge gained could help scale up production volumes in the medium to long term.
Holistic approach
Mercedes-Benz takes a holistic approach to the circularity of battery systems and considers three core topics: circular design, value retention and closing the material loop.
With its Design for Circularity approach, the OEM is taking the entire battery technology value chain into account from the outset. At the Mercedes-Benz eCampus in Stuttgart-Unterturkheim, which opened in 2024, circular thinking flows into the development of new battery cells. Battery production for electric Mercedes-Benz vehicles is net carbon-neutral in battery factories on three continents. Local battery production is a key factor for the success of the Mercedes-Benz sustainable business strategy.
In line with circular thinking and to conserve resources, the company offers reconditioned batteries as spare parts for all its electric vehicles. In addition, its Mercedes-Benz Energy subsidiary has established a successful business model with large-scale stationary storage applications. Batteries that are no longer suitable for vehicle use can enjoy a second life as part of an energy storage system.
Jorg Burzer, Member of the Board of Management of Mercedes-Benz Group, responsible for Production, Quality & Supply Chain Management stated “We are systematically deepening our expertise in the battery value chain. Following the opening of the Mercedes-Benz eCampus for development of new battery cell chemistries in Stuttgart-Unterturkheim, we are now sustainably closing the raw materials loop in Kuppenheim. The innovative technology enables us to recover valuable raw materials from the battery with the highest possible degree of purity. This turns today's batteries into tomorrow's sustainable mine for raw materials. The new battery recycling plant strengthens the role of the Mercedes-Benz production network with vehicle and drivetrain plants in Europe.”
Thekla Walker MdL, Minister for the Environment, Climate and Energy Baden-Wurttemberg said, “Battery recycling is of great importance to Baden-Wurttemberg as a state with such a strong automotive sector. Closing the loop on the value chain reduces dependencies, increases resilience in times of crisis and can smooth peaks and troughs in the availability of raw materials. Mercedes-Benz is a pioneer in this respect: With the integrated battery recycling plant, Mercedes-Benz has developed a sustainable approach for dealing with limited resources and is therefore making a valuable contribution to a truly circular economy. We are proud that in this federal state of innovators, we are also at the forefront in this field.”
Euler Motors Enters E-Autorickshaw Segment With Neo
- By MT Bureau
- August 26, 2025
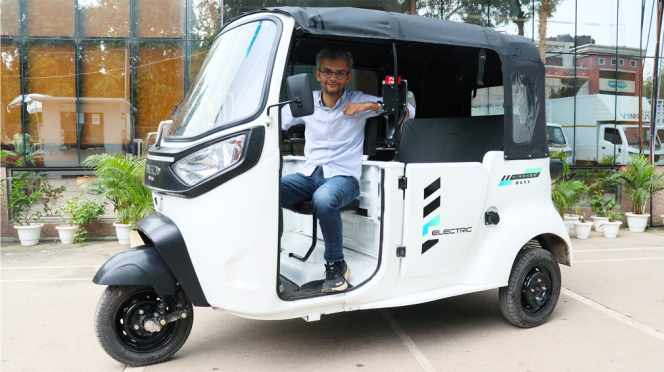
Delhi-NCR-based electric vehicle maker Euler Motors has entered the electric three-wheeler passenger category with the 'Neo by Euler' brand.
The company introduced the first vehicle under this brand, the Neo HiRANGE electric three-wheeler, with an introductory price of INR 309,999. The vehicle is designed for last-mile passenger transport in cities.
The vehicles under the 'Neo by Euler' brand will serve a range of customers, including new EV buyers, drivers for ride-hailing services, fleet operators and self-employed owners. Euler Motors plans to roll out these vehicles across 50 Indian cities over the next three to four months.
Euler Motors states that autorickshaws are a vital part of urban transport in India. Its new EV, the Neo HiRANGE, addresses the need for reliable, long-range and durable vehicles in this sector. The company's two years of research and development, which included conversations with over 10,000 auto-rickshaw drivers, shaped the vehicle's design. The Neo HiRANGE is built for Indian roads, with a rugged chassis and real-time diagnostics.
The vehicle comes in three variants: Neo HiRANGE Maxx, HiRANGE Plus and HiRANGE. The top variant offers a range of over 200 km on a single charge and can be charged in 3.25 hours. It has a skateboard chassis, 65 Nm of torque and hill-assist for stable performance. The vehicle includes a warranty of up to six years or 175,000 km and an anti-theft GPS system.
Saurav Kumar, Founder and CEO, Euler Motors, said, "We are excited to enter the commercial passenger EV segment. 'NEO by Euler' reflects our proven leadership in the commercial EV market. It is the result of deep product learning and on ground engagement with auto drivers across Indian cities. We heard firsthand challenges faced by drivers every day, from long fuel queues and unreliable maintenance to passenger discomfort, and low savings. These insights have shaped every aspect of the brand. Drivers want a solution that offers the highest range in a single charge, supports their livelihood, and gives them the confidence to keep moving. 'Neo by Euler' is our response to those needs; a no-compromise brand built for the realities of commercial passenger mobility in India offering best in class passenger comfort, consistent earning to drivers and overall safe solution."
Ola Electric Gets PLI Certification For Gen 3 Scooter Portfolio
- By MT Bureau
- August 26, 2025

Bengaluru-headquartered electric vehicle company Ola Electric has announced that it’s Gen 3 e-scooter portfolio has received Certification for Compliance under the Production Linked Incentive (PLI) Scheme for the automobile and auto components sector.
The certification granted by the Automotive Research Association of India (ARAI) will allow Ola Electric to receive incentives from 13 percent to 18 percent of the determined sales value (DSV) until 2028.
At present, the company’s Gen 3 portfolio comprises of S1 Pro 3 kWh, S1 Pro 4 kWh, S1 Pro+ 4 kWh, S1 X 2 kWh, S1 X 3 kWh, S1 X 4 kWh and S1 X+ 4 kWh.
“Securing PLI certification for our Gen 3 scooters, which form the bulk of our sales, is a critical step towards profitability. This will directly strengthen our cost structure and margins, enabling us to deliver sustainable growth. With our auto business targeted to turn EBITDA positive, the certification acts as a strong catalyst to achieve that goal while ensuring our customers continue to get the best-in-class EVs at highly competitive prices,” said a Ola Electric spokesperson.
BMW Group India Drives Past 5,000 EV Deliveries, Establishes Charging Network Over 4,000km
- By MT Bureau
- August 22, 2025
German luxury automotive brand BMW Group India has cemented its leadership in the luxury electric vehicle (EV) market by becoming the first in the segment to deliver over 5,000 EVs in the country. To mark this significant milestone, the company has inaugurated a new high-power charging corridor spanning 4,000 kilometres from North to South, offering charging access to all EV brands.
The new corridor features charging stations every 300 kilometres, effectively linking major cities and highways from Jammu to Madurai. The route covers key locations including Delhi, Jaipur, Ahmedabad, Mumbai, Pune, Bengaluru and Chennai, aiming to eliminate range anxiety for EV drivers.
Vikram Pawah, President and CEO, BMW Group India, said, “BMW Group India is immensely proud to become the first luxury carmaker to cross the remarkable milestone of 5,000 electric vehicle deliveries. This achievement is not just a number, it represents our unwavering commitment to e-mobility and pioneering spirit in the premium EV landscape. At BMW, luxury and performance is delivered seamlessly with sustainability, and our electric products embody this philosophy. In this journey, we will continue to delight our customers with the most electrifying products and services that provide complete peace of mind. To mark this milestone, we are happy to introduce our high-power charging corridor. Across the length of the nation, from Jammu to Madurai, EV customers can now just sit back and enjoy Sheer Driving Pleasure without a second thought.”
In a move to encourage broader EV adoption, BMW Group India has made these new charging stations accessible to all EV owners, regardless of their vehicle's brand. The stations, with capacities ranging from 120kW to an impressive 720kW, are a part of a larger network of over 6,000 charging points across the country, accessible via the myBMW app. The company is collaborating with charging operators like Statiq and Zeon to manage these new stations.
The sales milestone has been attained by the company’s expansive portfolio of EVs compromising the flagship BMW i7 to the popular BMW iX1 Long Wheelbase, which was the highest-selling BMW EV in the first half of 2025.
TVS Motor Company Launches King Kargo HD EV, CNG Variant On The Cards Too
- By MT Bureau
- August 21, 2025
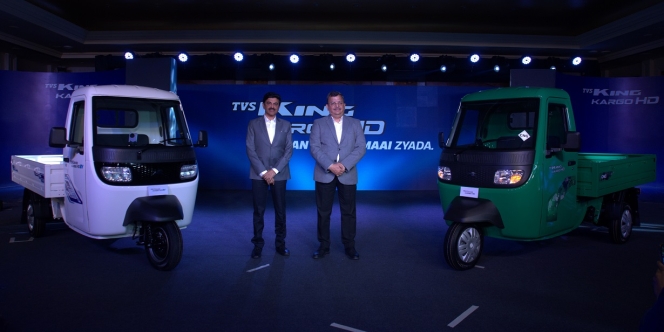
Chennai-headquartered two-wheeler and three-wheeler major TVS Motor Company has launched a new electric three-wheeler, the ‘TVS King Kargo HD EV’ at INR 385,000 (ex-showroom Delhi), which it believes will transform urban and semi-urban logistics. The EV is engineered for performance, durability and connectivity in the last-mile delivery sector.
The King Kargo HD EV is designed to improve safety and comfort for operators. It features several segment-first innovations, including LED headlamps and tail lamps for better visibility and a spacious cabin with fully rolling windows. For enhanced performance, it has a dedicated Power Gear Mode that provides higher torque when carrying heavy loads.
The new three-wheeler is also India's first Bluetooth-enabled cargo three-wheeler. It comes equipped with TVS SmartXonnect, offering 26 smart features, along with twin-axis rear-view mirrors for safer navigation through congested city streets. The vehicle’s connected features are managed through TVS Connect Fleet, a web-based platform that gives fleet operators real-time tracking, remote control and advanced analytics for efficient fleet management.
Rajat Gupta, Business Head of Commercial Mobility at TVS Motor Company, said, “The launch of the TVS King Kargo HD represents a transformative moment in the evolution of cargo mobility, aligned to our ‘Re-Imagine 2030’ vision. This three-wheeler will set new benchmarks by delivering an unmatched combination of smart features, high load capability, comfort, ergonomics and safety. Coupled with the TVS Connect Fleet, the vehicle will empower businesses and also improve the everyday life of operators. With the TVS King Kargo HD EV, we are confident of redefining customer expectations and enabling them to achieve more, every day, effortlessly.”
In its initial phase, the TVS King Kargo HD EV will be available in key markets, including Delhi-NCR, Rajasthan and Bengaluru. The company also showcased a CNG variant, which is scheduled for release later this year.
Comments (0)
ADD COMMENT