Layam Group Sees Strong Growth In Contract Manufacturing
- By Gaurav Nandi
- March 05, 2025
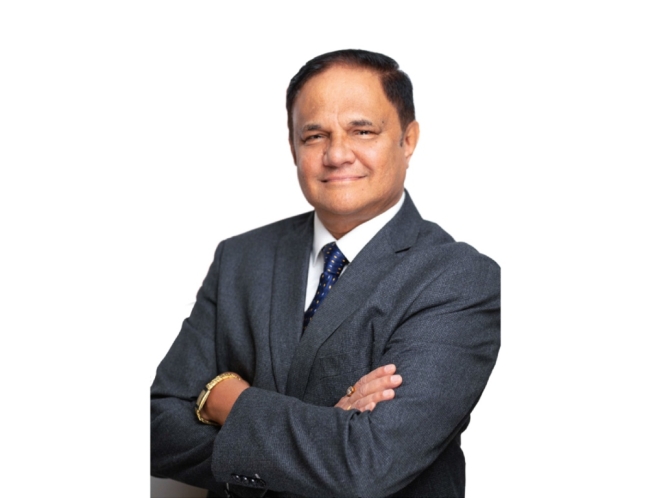
Increased demand and strategic shifts by global corporations are acting as growth factors for the sector. The home-grown automobile sector is also relying on this new-age trade practice as it allows companies to reduce capital expenditure on infrastructure, equipment and labour.
Different industries within India have found a fondness towards contract manufacturing owing to several factors. The sector is experiencing significant growth driven by increased demand and strategic shifts by global corporations.
Policies like ‘Make in India’ act as a catalyst for the growth by offering incentives to boost domestic manufacturing. The Central Government has also introduced measures to attract foreign investment in electric vehicle (EV) manufacturing, aiming to establish India as a hub for EV production.
The home-grown automotive sector is also seen relying more on this new-age trade practice. From commercial to passenger vehicles, contract manufacturing allows automakers to reduce capital expenditure on infrastructure, equipment and labour. Instead of investing heavily in setting up factories, companies can focus on product development, marketing and other areas while leveraging third-party manufacturers.
Speaking to Motoring Trends, Layam Group Chairman G S Ramesh said, “The automobile industry encompasses plenty of activities including assemblies, subassembly etc. Currently, there is a shortage of labour within the industry. Contract manufacturing is picking pace as it helps companies to offload certain responsibilities without compromising on quality standards.”
“Companies involved in contract manufacturing take full responsibility of the products and are extremely cautious about quality and skill aspects. They produce the products in tandem with set quality standards and get paid in return,” he added.
Companies involved in this model also cut back on employee costs as contractors hire their own workforce and are responsible for their career progression.
Layam Group is involved in automobile, smartphone and other sectors for contract manufacturing. It reported an INR 3-4 billion turnover with 70 percent revenue coming from the automobile and engineering sectors.
Commenting on the same, Ramesh explained, “We have been involved in the space for the past few years. We have undertaken two kinds of models. One is contract manufacturing, and the other is job contract model. In the job contract model, we assume the role of a third-party quality inspector of the contract issuer’s product line.”
Alluding to vehicle segments the company manufactures under contracts, he noted, “We are involved in the commercial vehicle segment, where we produce the body frame for Tata Motors’ buses. We produce electric buses too and are also involved in logistics, shell making, final panelling etc. The manufacturing unit is in Dharwad and Lucknow.”
Commenting on market opportunities, the executive noted, “India’s contract manufacturing sector presents a compelling growth story, driven by rising demand for trusted partners among OEMs and smaller manufacturers alike. The opportunity lies in how effectively firms can position themselves as reliable collaborators. Clients are increasingly open to outsourcing, provided they find dependable service providers, creating a strong business case for contract manufacturers.”
“Small and medium enterprises are also showing interest in contract manufacturing, seeking to integrate themselves into broader supply chains. This trend signals a growing ecosystem where even niche players can secure a foothold,” he added.
However, the key challenge remains a mindset shift. Traditional industry players often resist adopting technology-driven solutions, preferring conventional methods. Yet, once convinced, they integrate seamlessly, underscoring the importance of strategic engagement. The availability of skilled resources is less of a bottleneck, given the emergence of hire-train-deploy models that ensure workforce readiness.
“In an increasingly competitive landscape, transparency and trust emerge as the defining factors for success. Companies that establish credibility and deliver on performance expectations will secure long-term partnerships and growth,” said Ramesh.
Kinetic Engineering Upgrades Ahilya Nagar Facility With Robotic Chassis Line
- By MT Bureau
- September 03, 2025
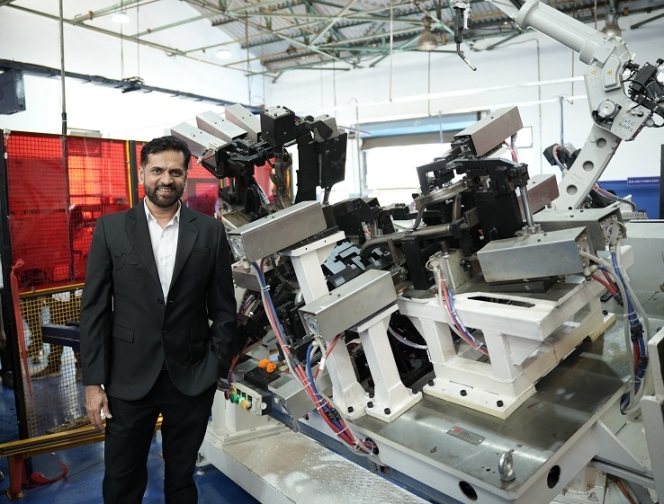
Pune-headquartered automotive company Kinetic Engineering has inaugurated its new Robotic Chassis Line at its plant in Ahilya Nagar, Maharashtra. This upgrade is part of a series of changes to improve the company's production capabilities.
The new line uses robots for welding and has a specific cell for the Kinetic DX EV e-scooter frames, clamping auto fixtures. This system is designed to provide consistency and accuracy. The facility's metal body panel line has also been upgraded with hydraulic and mechanical presses, as well as spot welding equipment.
The company's paint shop now uses a seven-tank process that includes a CED coating and a metallic topcoat for better protection and finish. A new store for frame parts has also been set up with quality control systems to manage inventory and supply parts to the assembly line.
Ajinkya Firodia, MD, Kinetic Engineering, said, “The future of manufacturing belongs to companies that can seamlessly integrate automation, precision and sustainability into their processes. With the inauguration of our robotic chassis line, we are not just upgrading a facility, we are reimagining how manufacturing should be done in India. This move positions us to deliver unmatched consistency and reliability, while also setting a benchmark for how automation can transform traditional industries. At Kinetic, we see this as part of a larger shift where Indian manufacturing stands shoulder to shoulder with the best in the world.”
Mukand Sumi Special Steel to Build New EUR 234M Integrated Steel Plant In Karnataka
- By MT Bureau
- September 01, 2025
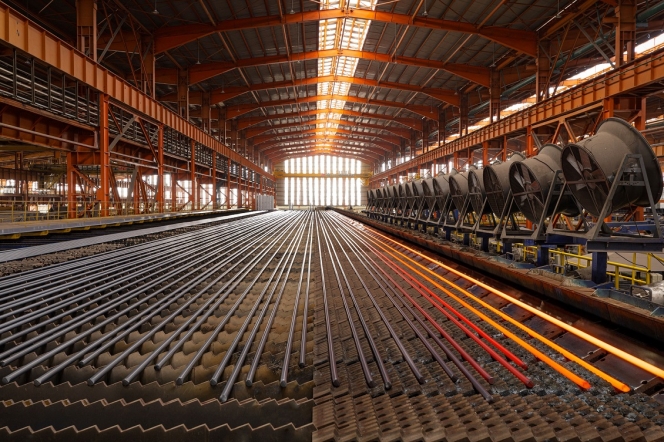
Mukand Sumi Special Steel (MSSSL), a joint venture between India’s Bajaj Group and Japan’s Sumitomo Corporation, has announced a major expansion with the construction of a new integrated steelmaking facility in Kanakapura, Koppal, Karnataka.
The new greenfield plant will boost MSSSL's production capacity to 700,000 tonnes per annum, making it one of India's leading special steel manufacturers. The project, which is currently awaiting environmental clearances, involves a capital investment of INR 23.45 billion, or around EUR 234 million.
The expansion is driven by the increasing demand for high-quality special steel in India's industrial, energy, and automotive sectors, supported by government initiatives like Atmanirbhar Bharat and strong economic growth. Since its inception in 2018, MSSSL has produced approximately 350,000 tonnes of special steel products annually, primarily for the automobile and engineering markets.
The new facility is designed with sustainability as a priority, adopting a Zero Liquid, Solid and Gaseous Discharge Model. It aims to source over 95 percent of its energy from renewables and is a crucial step towards the company's goal of achieving net-zero steel manufacturing by 2050. Future phases will incorporate hydrogen-ready infrastructure and carbon capture technologies.
Vipul Mashruwala, President, MSSSL, said, "This expansion marks a significant milestone in our long-term growth roadmap. Guided by the forward-looking vision of our Chairman, Niraj Bajaj, we are investing in sustainable and future-ready technologies that will strengthen our position in the global special steel market."
He added that the new facility will allow them to ‘serve growing demand with greater efficiency, quality, and environmental responsibility.’
The new plant is expected to begin operations by early 2028 and will include iron making, steel making, and blooming mill facilities with an initial capacity of 0.35 million tonnes per annum. The investment will also focus on integrating automation and digital technologies to ensure consistent product quality and optimised energy use.
The expansion will enable MSSSL to focus on critical applications in the automotive, railway, oil and gas, energy and bearing steel sectors, aligning with India’s ‘Industry 4.0’ initiative.
- Maruti Suzuki India
- Narendra Modi
- e Vitara
- TDS Lithium-Ion Battery Gujarat
- Suzuki Motor Corporation
- Toshihiro Suzuki
PM Modi Flags Off Maruti Suzuki’s First Made-in-India EV, e Vitara
- By MT Bureau
- August 26, 2025
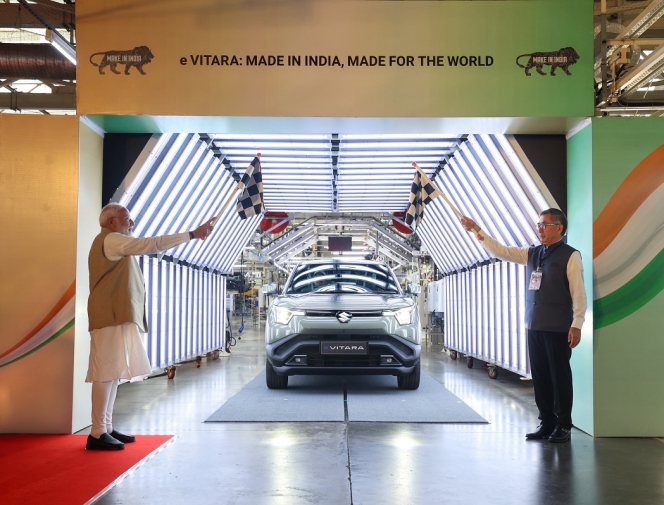
The Prime Minister of India Narendra Modi commemorated the start of production of Maruti Suzuki India’s first battery electric vehicle (BEV), the e Vitara, at Suzuki Motor Gujarat.
The model is being manufactured for both domestic sales and exports to over 100 countries, including markets in Europe and Japan. Maruti Suzuki India aims to produce 67,000 electric vehicles during FY2026.
At the same event, PM Modi also marked the start of local manufacturing of lithium-ion battery cells and electrodes for strong hybrid vehicles at TDS Lithium-Ion Battery Gujarat, a fellow subsidiary of Maruti Suzuki India. This makes TDSG the first company in India to achieve electrode-level localisation of lithium-ion battery cells, used in hybrid systems of models such as the Grand Vitara.
Maruti Suzuki said the e Vitara, built on a dedicated EV platform, will be India’s largest mass-produced and exported electric vehicle. The first export batch will be shipped via Pipavav port to European countries including the UK, Germany, France, Italy and the Nordics.
Toshihiro Suzuki, Representative Director and President, Suzuki Motor Corporation, said, “We are deeply honoured that Hon’ble Prime Minister graced the occasion of commemoration of two historic events for the Indian automobile industry. His inspiration and visionary leadership have made this possible. His vision of Make in India and Aatmanirbhar Bharat have been inspiring Suzuki to invest in India. These milestones are also a testimony to the enduring Indo-Japanese partnership, built on mutual trust and a shared vision for progress and a carbon neutral future. We will provide all products and technologies that will reduce oil consumption and imports and carbon emissions like battery electric vehicles, strong hybrid electric vehicles and vehicles powered by natural gas and biofuels.”
Suzuki has further announced that the automaker will invest over INR 700 billion in India over the next five to six years.
- JSW Sarbloh Motors
- JSW Defence
- JSW Group
- Tomcar USA
- ATV
- Parth Jindal
- Jaskirat Vladimir Singh Nagra
- Ram Zarchi
- Mark W. Farage
JSW Sarbloh Motors Partners Tomcar USA To Manufacture ATVs In India
- By MT Bureau
- August 21, 2025
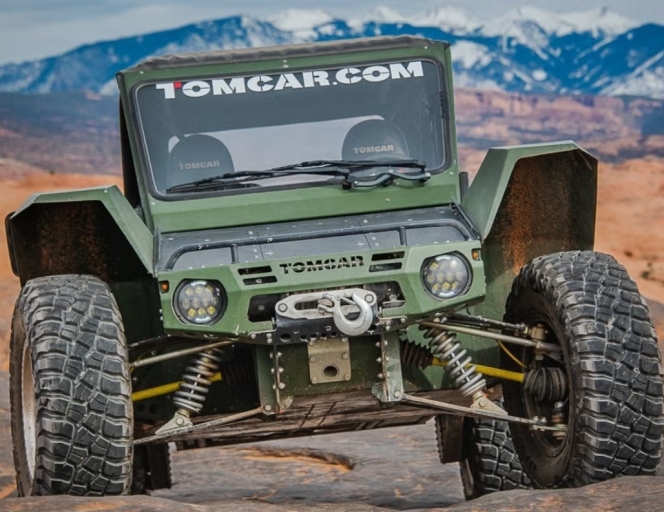
JSW Sarbloh Motors, a subsidiary of JSW Defence, a JSW Group company, has formed a strategic joint venture with Tomcar USA, a leading manufacturer of all-terrain vehicles (ATVs), for the local production of the TX range ATVs in India.
This partnership marks the expansion for JSW Group in the mobility space, especially for indigenous manufacturing of tactical mobility platforms for Indian Armed Forces, Central Armed Police Forces (CAPFs), State Police units and strategic industrial sectors requiring ultra-durable extreme mobility off-road platforms.
As part of the understanding, JSW Sarbloh Motors will indigenise, manufacture, assemble and support the Tomcar TX range at its facility in Chandigarh with the first product expected to be rolled out by early-2026, with field trials and demonstrations planned for multiple defence and paramilitary agencies in the coming months.
Parth Jindal of the JSW Group, said, "We are delighted to announce this strategic joint venture between JSW Sarbloh Motors and Tomcar USA, which marks a significant milestone in our commitment to enhance India's defence capabilities. The TX platform is designed to meet the rigorous demands of our armed forces and security agencies whilst ensuring superior durability, flexibility, and safety. At JSW, we believe in combining cutting-edge technology with local production capabilities to foster a robust industrial ecosystem that strengthens our national security and creates job opportunities.”
Jaskirat Vladimir Singh Nagra, CEO and Founder Director, JSW Sarbloh Motors, said, "This joint venture is more than a business partnership, it is a strategic alignment of vision and purpose. We are committed to offering India’s defence and industrial sectors world-class mobility platforms with the ruggedness, modularity, and reliability they demand. We look forward to this exciting collaboration and are confident that our joint efforts will set new standards in tactical mobility within India and beyond."
Ram Zarchi, Founder & Principal, Tomcar USA, said, "We are honoured to announce our strategic joint venture with the JSW Group, marking a pivotal milestone in Tomcar’s entry into India. This partnership will allow us to deliver our proven platforms to the Indian Armed Forces, combining Tomcar’s decades of mission-grade engineering with JSW’s advanced manufacturing expertise and first-class leadership. Together, we will strengthen India’s tactical mobility capabilities while expanding Tomcar’s global footprint, particularly into right-hand-drive markets.”
Mark W. Farage, Interim CEO, Tomcar USA, added, “This joint venture is the culmination of a thoughtful and deliberate process aimed at creating a truly strategic partnership. We are excited to hopefully contribute to India’s adaptation to the demands of modern warfare by providing the proven, battle-tested Tomcar platform to the Indian Army. In addition, we see enormous opportunity to deploy the Tomcar into India’s diverse commercial sectors – from mining and timber, to search and rescue, border patrol, farming, and beyond. This partnership positions us to deliver unmatched performance, durability, and reliability to customers
Comments (0)
ADD COMMENT